GUI¶
The user-friendly way to use the plug-in is through the graphic interface.
Just execute the file START_GUI.bat
.
You need Abaqus to be executable by the command line abaqus cae
for this to work.
The plug-in for Abaqus looks like this:
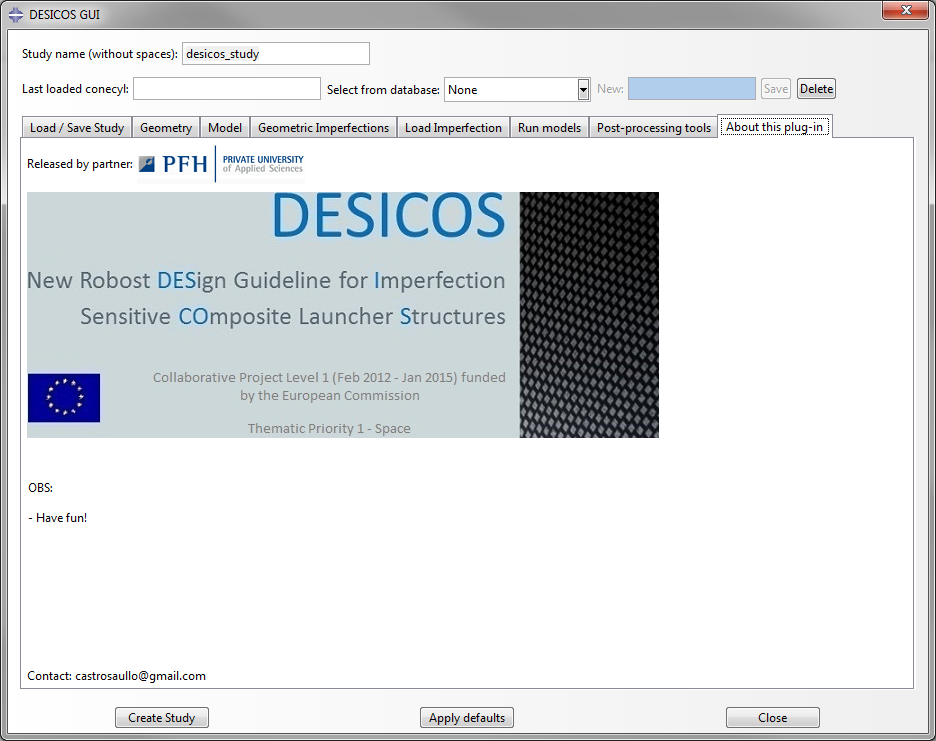
Loading and configuring a model¶
Where the desicos.conecylDB
is embedded, and the existing models
easily chosen from the Static Database or from the
Dynamic database. When the option
Enter New
is active, the buttons Save
is activated and
the user may save a new configuration into the database, which can
be deleted afterwards using the Delete
button.

Geometric parameters easily changed:
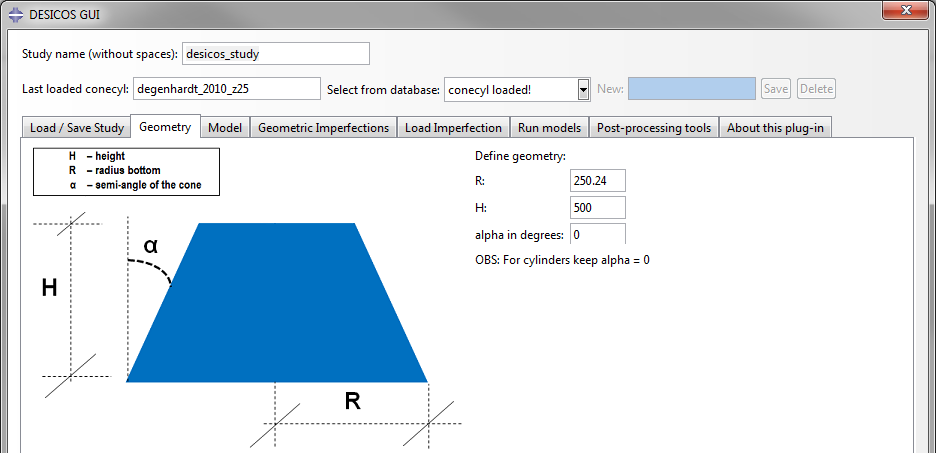
Material properties taken from the database and easily changed. Note that the
Dynamic database is implemented here through the use
of the buttons Save
(when the Enter New
option is active)
and Delete
.
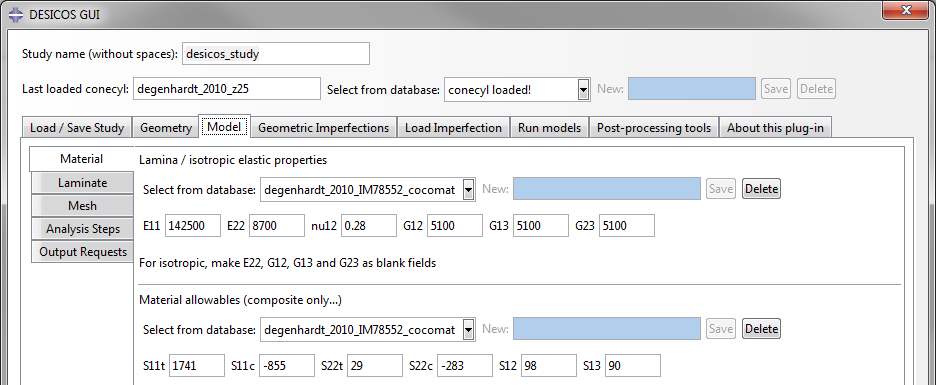
The laminate is defined giving a different material and thickness to each ply or defining only for the first ply when all the others should have the same material and thicknesses.
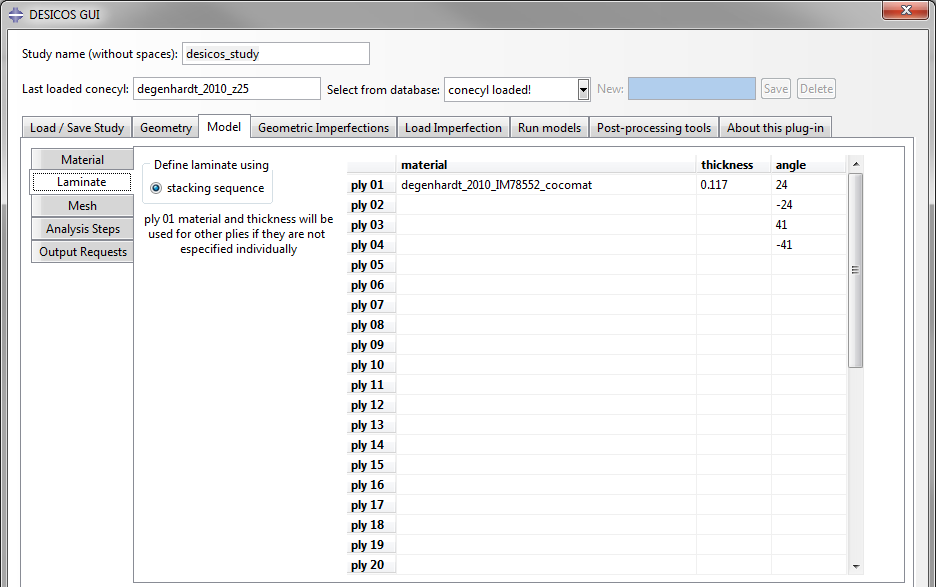
The mesh parameters are defined as shown below, and this data can also be saved and loaded in the database.
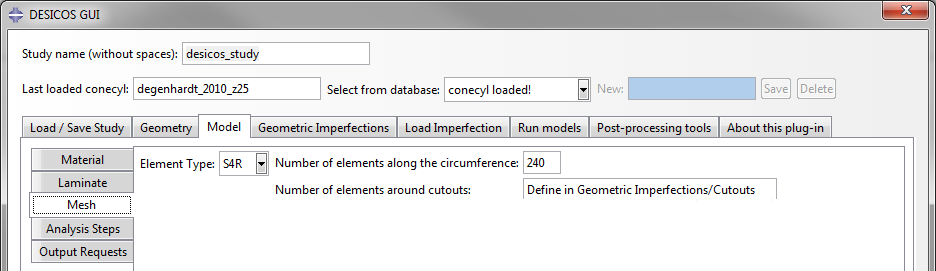
The analysis parameters are summarized as shown below. After the models are created the user may change those. This analysis’ configuration has been optimized for the Single Perturbation Load Approach (SPLA).
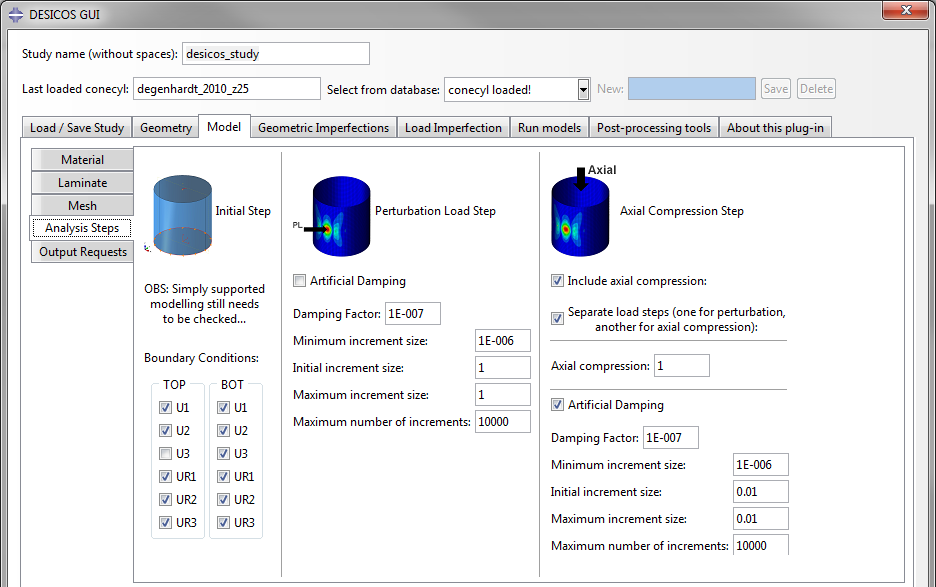
The number of output frames can be changed here, allowing some control
in the size of the output files. The Request stress output
checkbox
must be activated if one intents to perform a stress analysis:
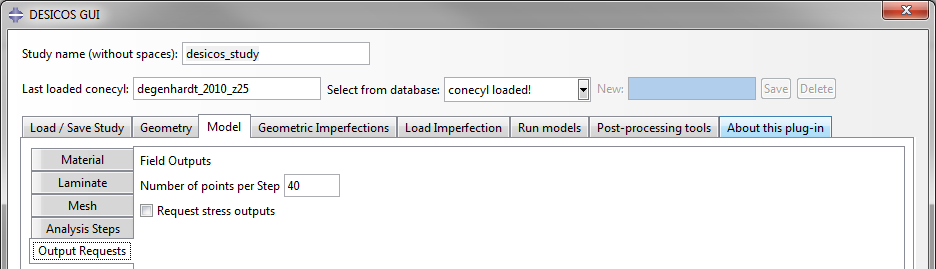
Applying imperfections¶
The perturbation loads can be applied using:
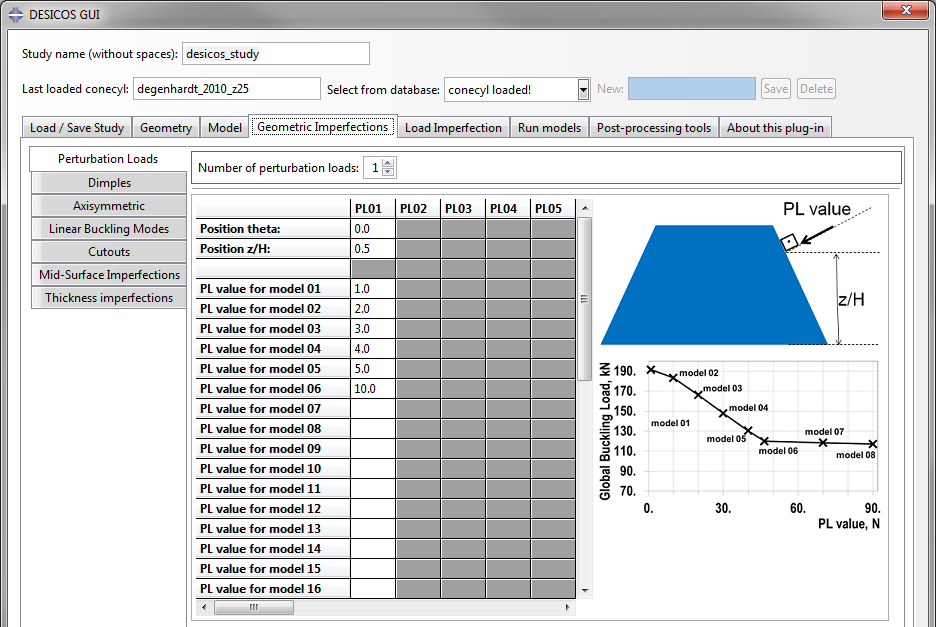
The geometric dimples using:
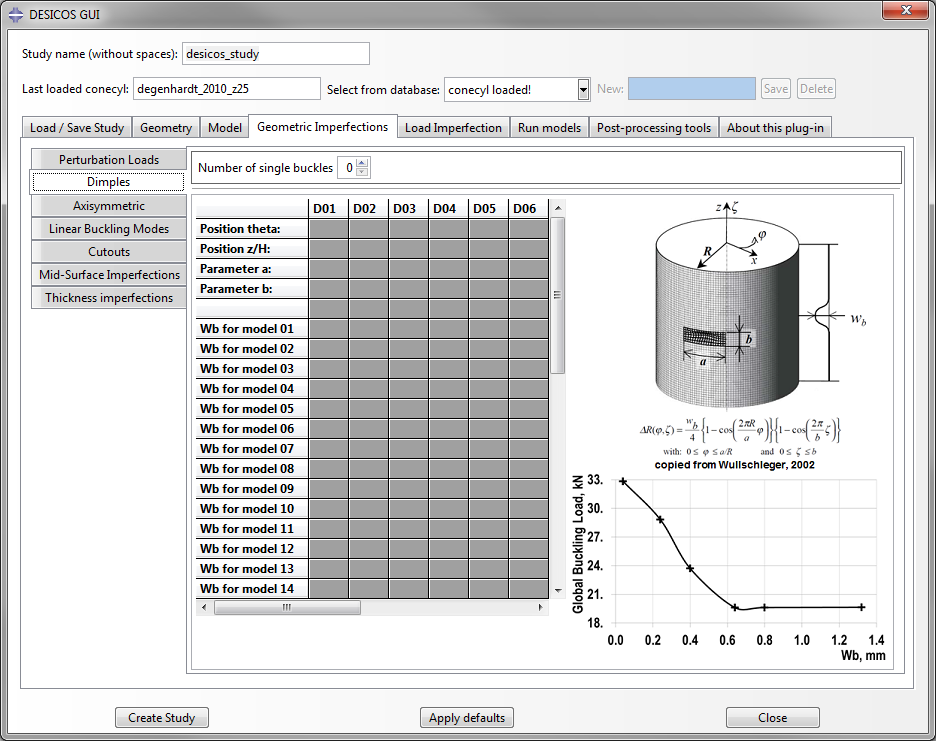
Axisymmetric imperfections:
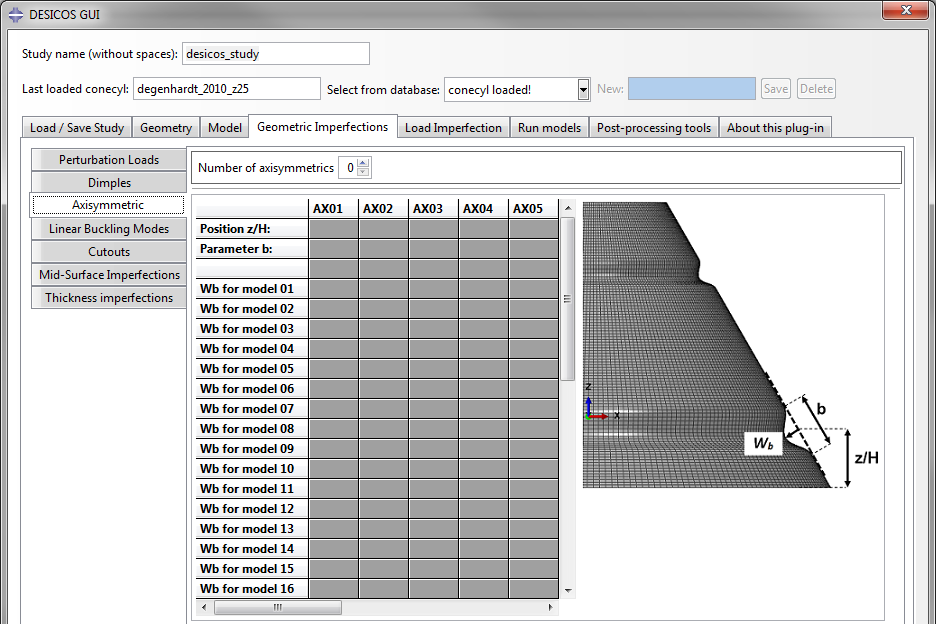
Imperfections from Linear buckling modes:
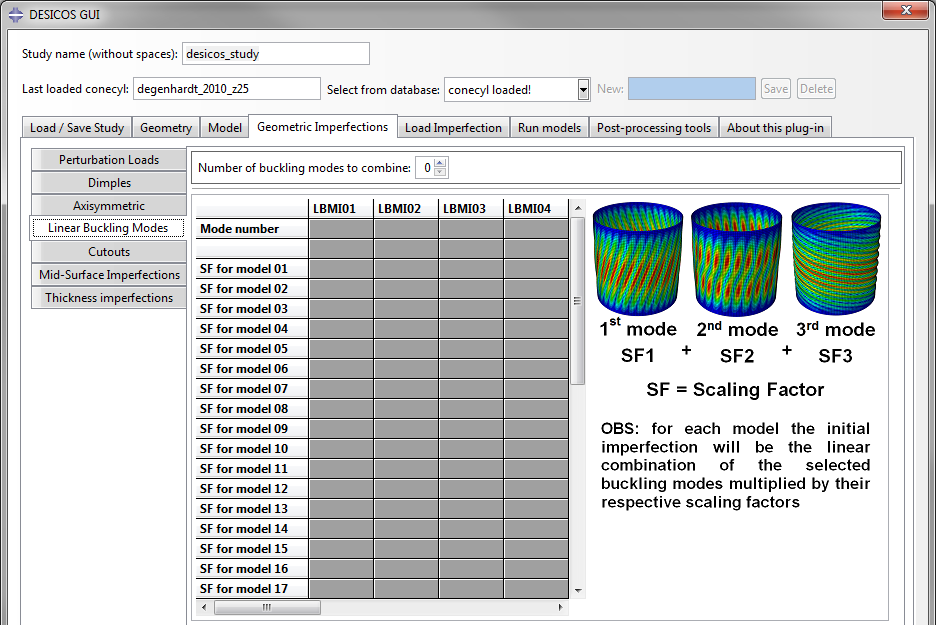
Cutouts:
Note
The cutouts module needs improvement!
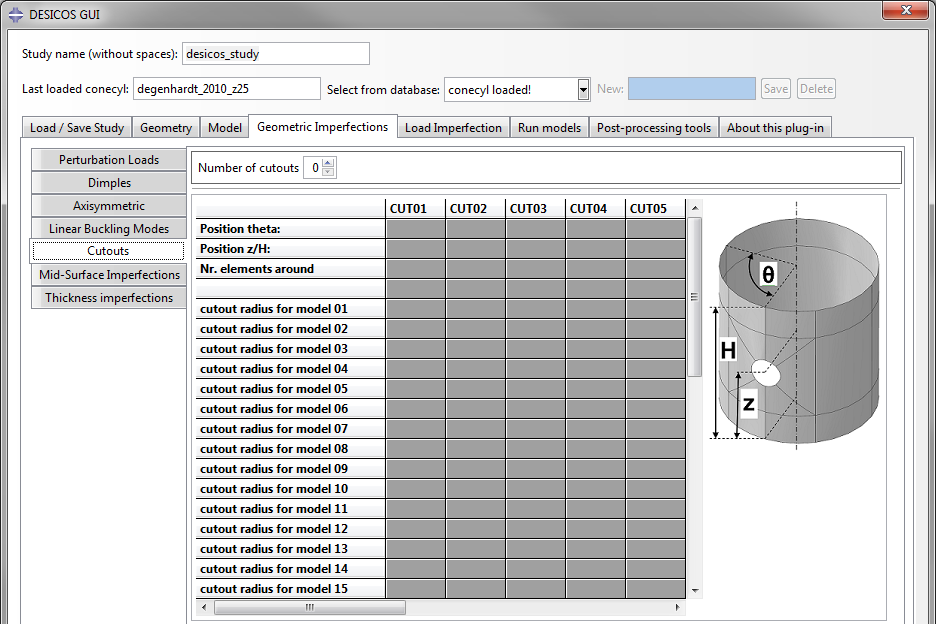
Measured geometric imperfections that represent the normal displacement of
the shell mid-surface can be applied too. This must be
applied after creating the study (click on Create Study
):
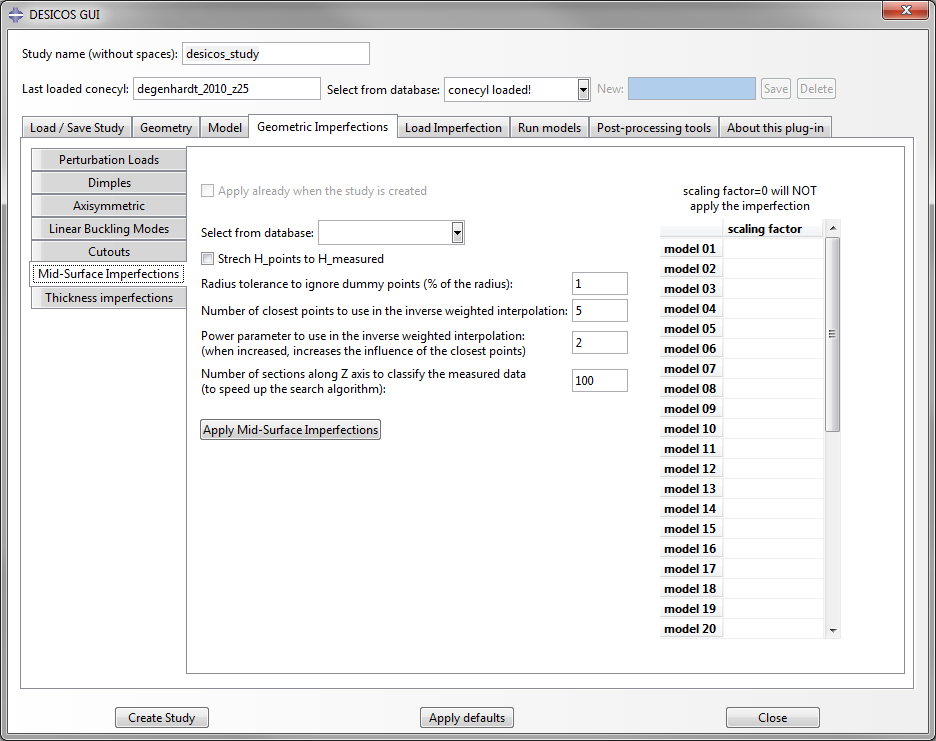
Similarly, thickness imperfections can be applied. If the study has not yet
been created, click on Create Study
before applying the thickness
imperfections:
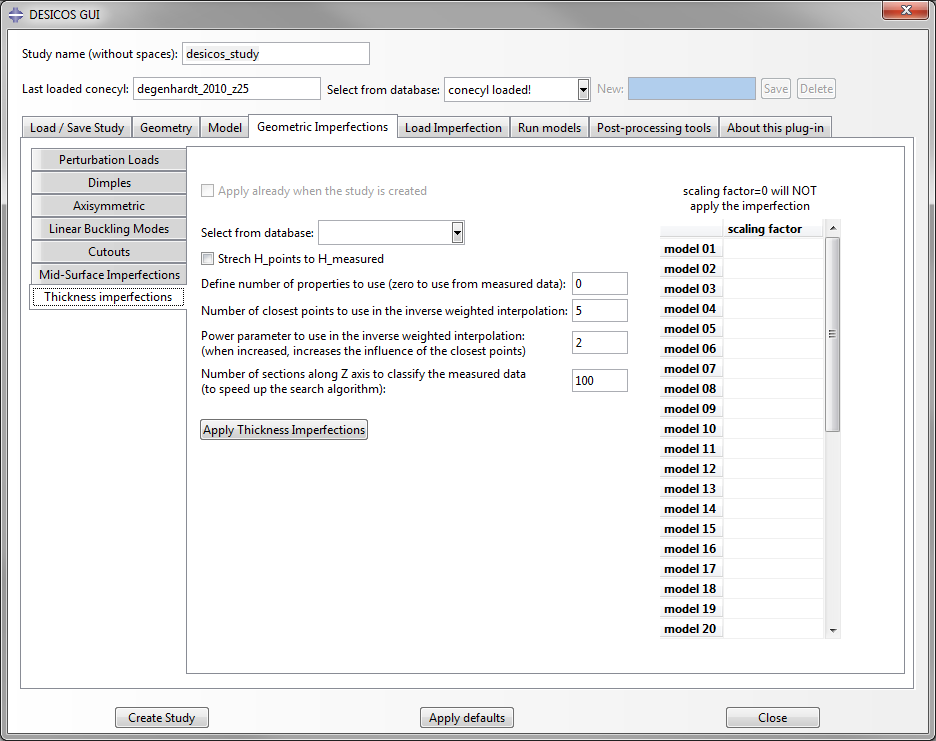
Load imperfections can also be considered:
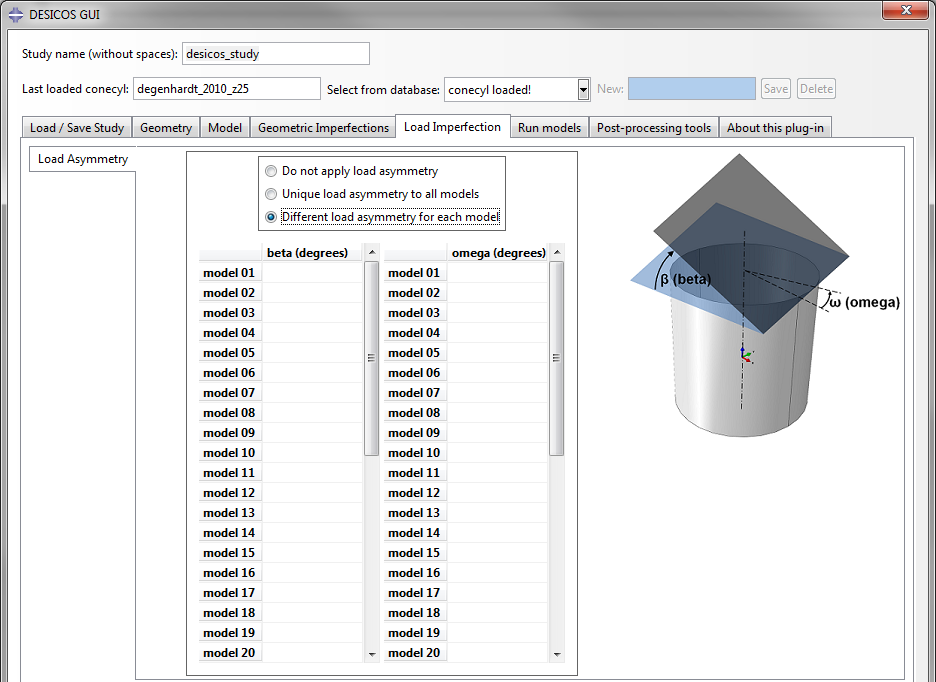
Running the analysis¶
It allows running the jobs in the structure of folders used by the plug-in
in order to keep the models organized. You can use multiple cpus
or
use the job stopper
, which significantly accelerates the analysis time
by stopping the analysis after buckling.
If the post-buckled pattern have to be studied, it may be better to run one
analysis with the job stopper
activated, obtain the axial compression
level that caused the buckling and then run another analysis disabling the
job stopper
in order to achieve the desired post-buckled pattern.
The run log file will be printed on the plug-in screen.
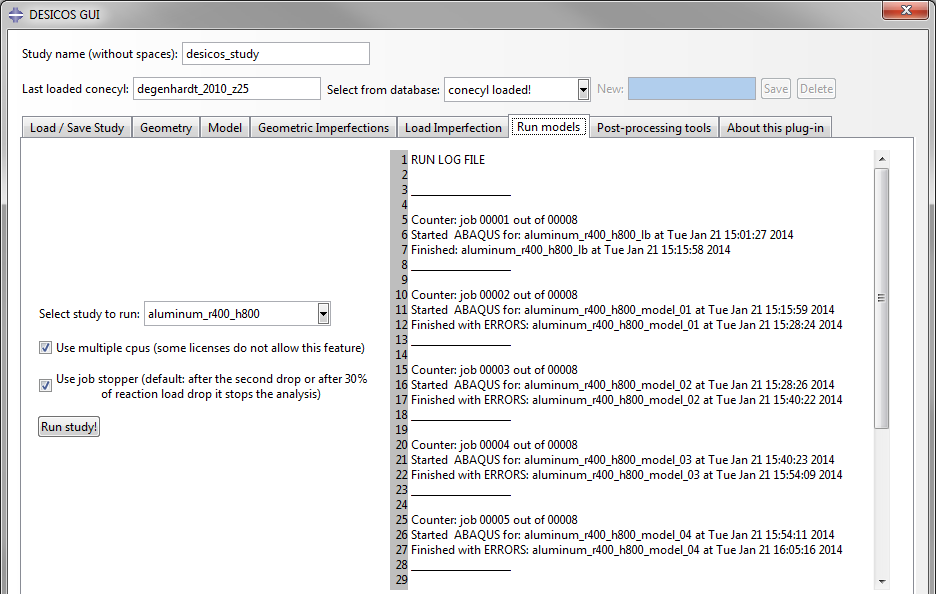
Post processing¶
For all the options you can add the results to an Excel file or even open the Excel after finished.
The load-shortening curves can be easily plotted:
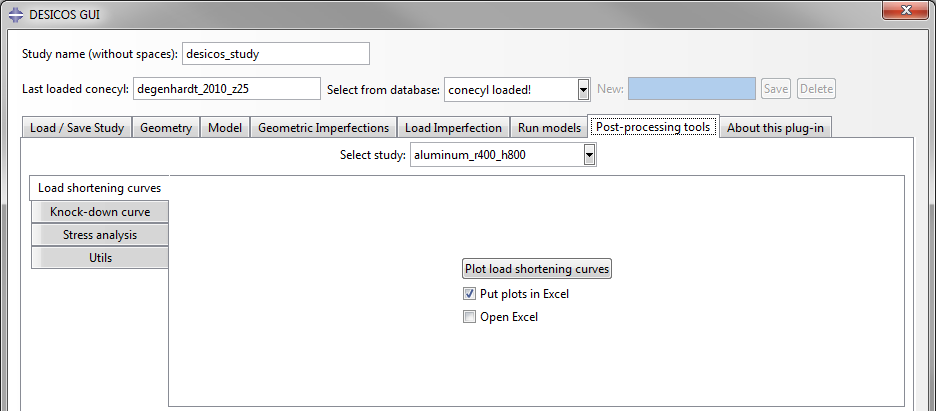
Or the knock-down curves:
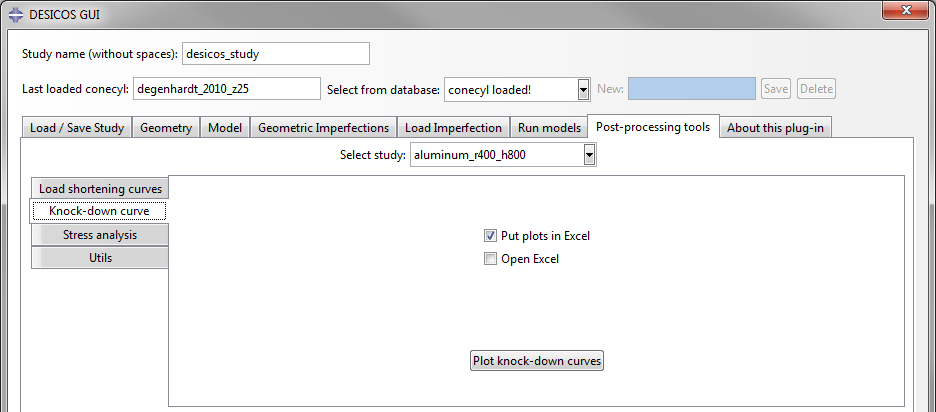
Or the stress analysis results:
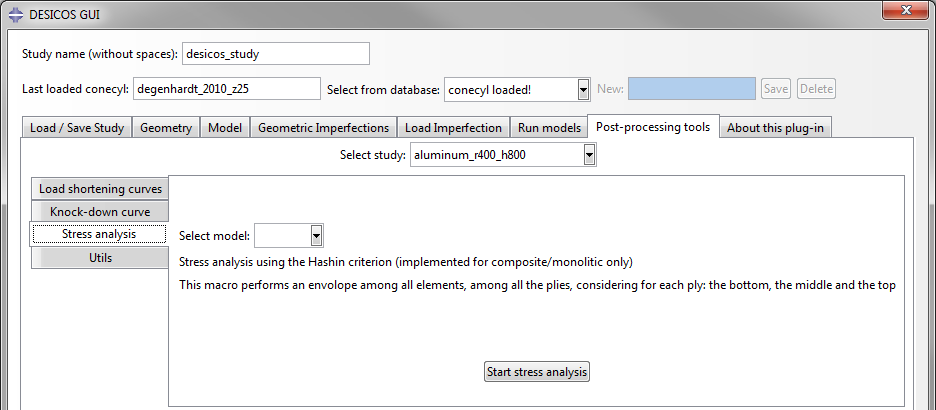
An extra options has been added to allow an opened representation of the cylinder or cone, convinient for publications:
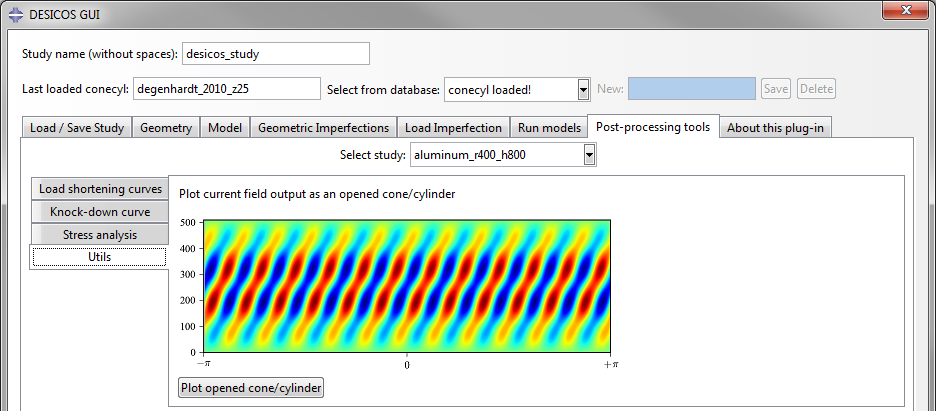